- HMPP winding storage tank production line
- PPH winding storage tank production line
- PP PE Plastic Welding Rod Production Line
- Plastic sheet production line
- PPH winding can mold
- PP vertebral body round head winding equipment
- Plastic sheet welding machine
- Plastic sheet bending machine
- Plastic sheet welding and bending integrated machine
- Plastic board carving machine
- Square internal and external welding automatic extrusion welding machine
- Automatic extrusion welding machine for inner and outer welding of round cans
- Plastic extrusion welding gun
- Plastic tank punching and cutting machine
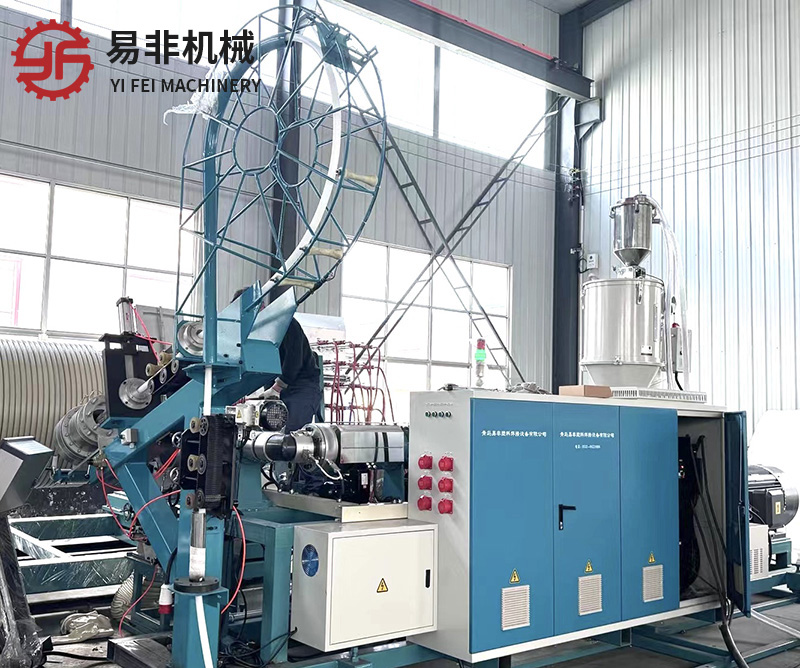
The HMPP winding tank production line can be used interchangeably with PPH winding equipment, and can simultaneously produce PP/PPH plastic storage tanks and HMPP three-layer winding sandwich tube cylinders. HMPP wrapped storage tank products are mainly used in the production of integrated prefabricated pump stations for sewage treatment. It is a new type of environmentally friendly material. The pump station cylinder is made of high modulus polypropylene material, which is biodegradable, environmentally friendly, and pollution-free. The cylinder wall adopts a three-layer wrapped intermediate sandwich pipe structure, and the product has high impact strength and good pressure resistance, suitable for burial. The installation cycle is short, and due to high integration, the installation and commissioning time of this pump station is significantly shortened compared to traditional pump stations.
The main processes include tank extrusion winding, demolding, external welding, internal seam welding, and pipe installation.
(1) Can body extrusion winding production: The process of extruding the first layer of granular material sheet, the second layer of PP clamp tube, the third or fourth layer of granular material sheet, and then winding them in sequence on a steel mold to form the can body. (2) External welding production: External welding is the process of using an automatic extrusion welding unit to weld the storage tank to the bottom of the tank in one welding process. Hot melt new granular material with the same properties as the tank body at the weld seam, and weld it together with the bottom and tank body. (3) The principle of internal welding is the same as that of external welding. Complete the internal welding work of the tank bottom in one go, increase the compression capacity of the tank bottom, prevent leakage, and effectively extend the service life of the product. (4) Finally, install the pipe openings and other components.